PET plastic packaging is a knowledgeable industry. In order to fully understand it, we are also constantly researching and learning, and the following is the key information of PET plastic packaging bottles that we have summarized.
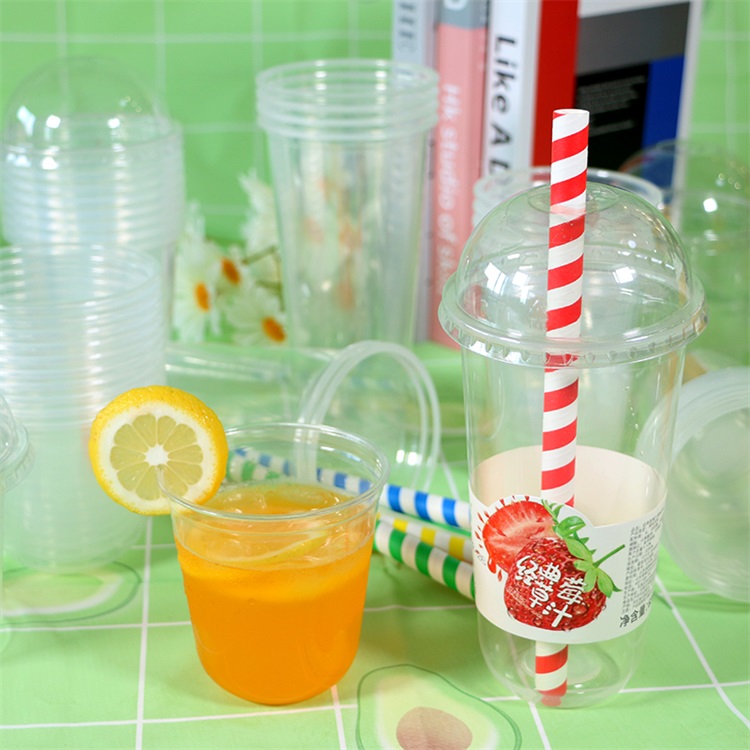
1. All plastics are derived from petroleum.
2. All plastic products have different colors, the technical core of plastic products is to prepare different colors.
3. The materials of plastic packaging bottles can generally be divided into PP, PE, PET, HDPE and acrylic.
4. One-step PET bottle production process: polyester raw material – drying – plasticization – tube blank injection molding – temperature adjustment – stretch blow molding – demoulding – inspection – finished product.
5. Cost of plastic products: plastic weight + mold cost + auxiliary materials electricity cost + labor cost.
6. Teeth refers to the size of the mouth of the bottle with teeth. The most common teeth are: 18 teeth, 20 teeth, 24 teeth, 28 teeth and 32 teeth. The wide mouth has 47 teeth, 53 teeth, 68 teeth and 89 teeth. The teeth mouth stated by the manufacturer is about 0.3-0.5mm larger than the actual measured diameter.
7. You can tell whether it is PET by smelling it. Burn it with a lighter. Pure pet plastic will emit a very fragrant smell. If PET plastic contains other ingredients, the smell will be very pungent.
8. Common printing processes for PET packaging bottles include: silk screen printing, labeling, laser engraving, laser engraving, bronzing, etc.
9. If the manufacturer’s existing male mold is used, the price will be lower, and the mold opening fee will be paid for independent mold opening.
10. Our production base has international standard GMP workshops, automated production lines, professional R&D and design centers, and a complete production management system. Large quantities and small quantities will never affect the quality of product production.